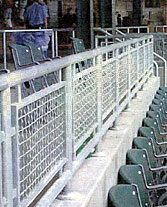
Some fabricated assemblies may distort at the galvanizing temperature as a result of the stresses induced during manufacturing of the steel and in subsequent fabricating operations.
To minimize distortion, design engineers should observe the following recommendations:
- Where possible, use symmetrical rolled sections in preference to angle or channel frames. I-beams are preferred to angles or channels.
- Use parts in an assembly that are of equal or near equal thickness, especially at joints.
- Bend members to the largest acceptable radii to minimize local stress concentration.
- Accurately perform members of an assembly so that it is not necessary to force, spring or bend them into position during joining.
- Continuously weld joints using balanced welding techniques to reduce uneven thermal stresses. Staggered welding techniques to produce a continuous weld are acceptable. For staggered welding of 1/8 inch (3.18 mm) or lighter material weld centers should be closer than 4 inches (10.16 cm).
- Avoid designs which require double dip galvanizing or progressive galvanizing. It is preferable to build assemblies and sub-assemblies in suitable modules so that they can be immersed quickly and fully in a single dip. In this way, the entire fabrication can expand and contract uniformly. Where double dip or progressive galvanizing is required, consult with your galvanizer if you anticipate a wide variance of section size.
- Consult with your galvanizer regarding the use of temporary bracing and/or reinforcing to minimize or prevent warpage and distortion during galvanizing.
Guidelines for minimizing distortion warpage are provided in ASTM Recommended Practice A384, “Safeguarding Against Warpage and Distortion During Hot-Dip Galvanizing of Steel Assemblies” and CSA Specification G164, “Hot Dip Galvanizing of Irregularly Shaped Articles.”
Back to list