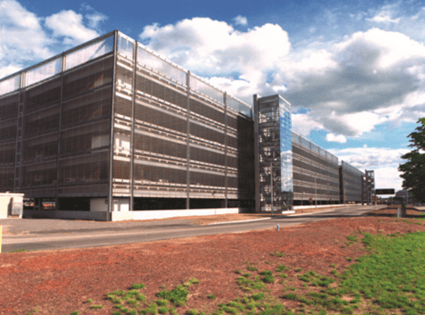
Steel is an exceptional building material. It has come into its own as a recognized, aesthetically pleasing part of the built environment. Since parking garages are no longer viewed simply as secondary structures in a project’s master plan, there is a need for a well designed architecturally impressive building. By working together, the entire building team can create work that is cost effective, long lasting, and beautiful.
Unfortunately, most areas where fabricated steel products are used are subject to hostile atmospheric conditions or direct contact with aggressive chemicals. Deicing salts, vehicle emissions and acid rain are the most common culprits. For the steel to last and do its designed work, it must be protected from this corrosive attack.
Hot Dip Galvanizing has been protecting steel from corrosion for centuries. Galvanizers understand the problems and have developed creative solutions. The problems of the parking industry are severe, but solutions achieved in other industries have enabled galvanizers to meet the challenge.
Some of the advantages of hot dip galvanizing in parking structures are:
-
The life expectancy of hot dip galvanized coatings is a proven, measurable factor. As zinc protects steel by sacrificing itself, the life of the coating can be accurately predicted by dividing the existing coating thickness by the average coating loss per year. The longevity calculations are based on empirical data, not theoretical. The result is the life to first rust (not failure). In most cases, the calculated life of most areas exceeds 40 years.
-
Hot dip galvanizing has been extensively used in the industry. Sign supports, landscape components, highway architecture, noise barriers and many other items are currently specified to be galvanized.
-
When galvanized, the galvanizer has sole responsibility for the coating system. As no recoat will be required, the problem of "mixed systems" for maintenance doesn't occur. Maintenance of records for prior coatings is simple ---it was galvanized.
-
The coating adherence and quality are simple to inspect and verify. If the base steel isn't properly cleaned and prepared, it will not coat. Hot dip galvanizing is the only corrosion protection system that guarantees that the steel is perfectly clean before application of the coating. There cannot be a metallurgical bond between the steel and zinc unless the steel is 100% contaminant free.
-
Hot dip galvanizing is the only system available that protects the steel on the inside as well as the outside. This is especially important in the case of tubular materials which cannot be maintained on the interior. Left untreated, the corrosion can rapidly spread from the interior of the tube to the outside ultimately resulting in a structural failure of the component. By coming in contact with moisture, the untreated steel will "bleed" onto the ground, concrete or other appurtenance. Occurring long before a loss of structural integrity, however, will be an aesthetic failure.
-
Galvanizing is a factory process and is not dependent on weather or other external conditions. This allows fabricators and contractors the ability to accurately schedule site deliveries, erection times and eliminate delays.
There is an inherent difference between hot dip galvanizing and other protective coating systems. Basically, steel is protected from corrosion through either barrier or cathodic methods. Barrier protection occurs when the protective mechanism acts to prevent the steel from coming into contact with the contaminant. How well it does its job is totally dependent upon the three “legs” of the coating triangle: Surface Preparation, Application, and Material. If the steel has not been prepared properly or if the application is done in less than ideal conditions, the coating will fail and corrosion will result. Paint is one example of the barrier method.
Cathodic protection is a process whereby the metal is protected from corrosion by changing an element of the corrosion circuit. A form of cathodic protection is called the sacrificial anode method. In this system, a metal that is anodic to the metal to be protected is introduced into the corrosion circuit and becomes the anode. The protected metal then becomes the cathode and will not corrode. Zinc is anodic to iron and steel and by forming a metallurgical bond between the coating and the underlying steel, hot dip galvanizing provides cathodic protection as well as barrier protection.
Furthermore, since the hot dip galvanizing process calls for the steel to be immersed into a bath of molten zinc and other earthly metals, it is being protected on 100% of its surface. This protection is critical and unavailable in other types of corrosion protection. It really serves no useful purpose to have a wonderful design, fabricated perfectly, with "rust bleed" staining the steel or adjacent material. This discoloration will lead to the public’s perception of inferior workmanship and lack of maintenance. As much attention must be paid to this particular issue as to the proper fabrication techniques. Since many garage components are tubular, it is important to specify a corrosion protection system that will not only protect the steel on the outside, but on the inside as well. In addition to providing corrosion protection, galvanizing’s pleasing gray color meets many visual requirements as well. Typically, galvanized steel will oxidize to a uniform patina. However, when the need for color is required for safety reasons or the design calls for a particular color scheme, galvanized steel can be successfully topcoated.
Contact Duncan Galvanizing
By following a proven formula, Duncan can add the beauty and additional longevity of a high performance coating system over galvanizing. For more information on the available paint and powder coating systems, and their warranties, please contact us at 617-389-8440 or fill out a contact form.